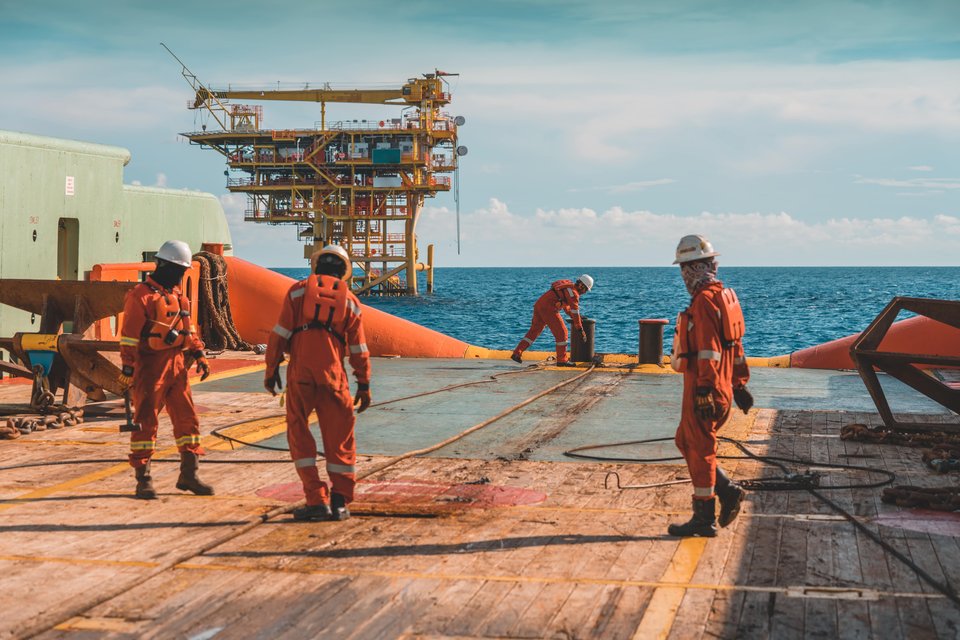
At BSM, safety is a top priority and we never compromise on it. Unfortunately, there are accidents outside our company that have resulted in the loss of lives; let’s ensure these are not repeated on our fleet.
Fatal Fall From Ladder
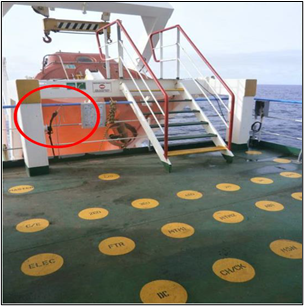
A ship, enroute to Los Angeles was preparing for the USCG inspection. The C/O instructed the Bosun to de-rust and paint the corroded turnbuckle and the securing pin for the free-fall lifeboat. Bosun assigned this job to an AB.
No work permit was issued as the work site was at one metre height and secured by railings. The C/O carried out only a verbal risk assessment. He had instructed the crew not to carry out any work aloft due to moderate rolling.
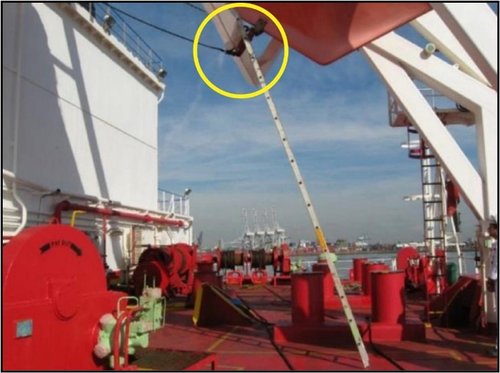
While performing the task, the AB observed that the forward hook for the free-fall lifeboat needed lubrication. AB requested the Bosun to assist him by steadying a portable ladder to reach the forward hook. The height from the deck to the forward hook was 4.8 metres. The ladder was 5 metres long.
The AB climbed up the ladder neither securing it nor using any PPE. The Bosun tried to hold the ladder in place however, was not able to control it. The AB fell along with the ladder and ended up motionless on the deck. He was tragically pronounced dead 3 hours later.
Consequences
- Fatality
- Delays
- Reputation of the company
Causes
- Failure to follow procedures:
- Lack of risk assessment and work permit – Although the working aloft procedures in the company’s SMS required a risk assessment and work permit to be prepared, these were not completed before starting work
- Use of unsafe equipment – The portable ladder was inappropriate for the task. The poor condition of the ladder feet meant both the legs were not in contact with the deck. The fact that ladder was not safely secured probably contributed to the ladder slipping and the AB falling off it
- Lack of PPE – The AB did not use proper PPE while climbing the ladder, as required by company procedures (e.g. safety helmet with chin strap, safety harness and fall arrester). This would have offered some protection to the AB when he fell and may have reduced the severity of his injuries:
- Inadequate monitoring, casual approach:
- Lack of intervention – The Bosun could have prevented the incident if he had stopped the job rather than assisting the AB to steady the ladder. Stop Work card provide crew members with the responsibility and obligation to stop work in case of an apparent unsafe condition or behaviour.
- Complacency – Completing a task not requiring a work permit, led the AB to assume that it would be acceptable to also lubricate the hook without a permit. Complacency can lead to shortcuts from established safe work procedures to save time and effort, but it can also lead to undesirable consequences.
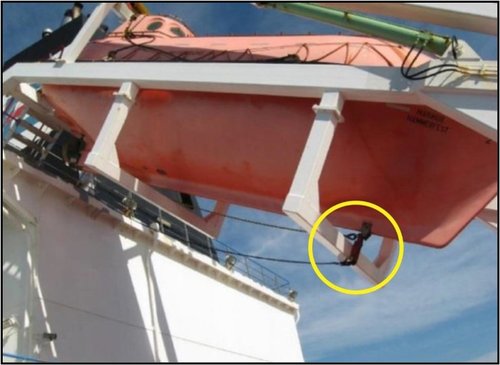
Lessons learnt
- Make use of the “Stop work card” when a colleague or a group of colleagues do not follow safe working practices.
- Strictly comply with company procedures of risk assessment, work permit etc. while working at heights.
- Ensure that all equipment is in good condition and used properly. Portable ladders must:
- Be secured properly.
- Be placed on stable surfaces at correct angles (between 60 deg and 75 deg. from the horizontal).
- Have anti-skid foot cap.
- Extend at least 1 m above the upper landing area.
- Always use appropriate PPE while working.
Death Due to Burn Injuries
The C/E decided to clean the “Waste Oil Settling Tank” (WOST) to repair a malfunctioning level indicator. He carried out the RA for the tank cleaning operation and assigned the job to the 2/E and 3/E.
The 2/E drained the WOST by gravity to the “Bilge Separator Oil Tank” (BSOT) through the drain valve. The 3/E turned the wire wheel of the scale reduction device on the top of the WOST and reported it was working. The 2/E opened the self-closing water drain valve and observed only a small quantity coming out. Based on above indications, the 2/E concluded that the WOST was empty.
The 3/E climbed on a folding ladder to remove the manhole cover located at a height of about two metres. He removed most of the nuts from the manhole except four nuts diagonally across from each other. He then loosened the last 4 bolts by half a turn. As there was no further oil leakage, he loosened the remaining nuts further. Without removing the nuts, he pulled the cover which detached from the seat. The hot oil of approx. 86°C splashed from the manhole bottom onto the 3/E.
The 2/E pulled away the 3/E and removed his coverall soaked with the hot oil. Crew brought the 3/E to the ship’s hospital and gave him first aid. He had sustained serious burns to various areas of his body. The Master requested a medevac through the local agent. The 3/E himself boarded the helicopter which took him to the local hospital. However, the 3/E died 12 days later at the hospital due to septic shock.
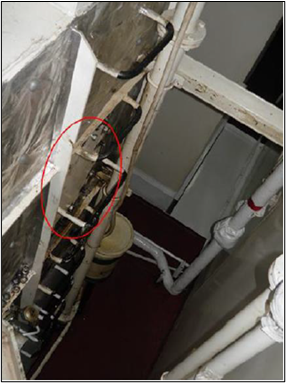
Tank manhole at two meters height
Consequences
- Fatality
- Delay
- Loss of company reputation
Causes
- Improper risk assessment: Not identifying the potential hazards related to the unknown quantity of hot sludge remaining in the tank due to the malfunctioning level gauge.
- Making assumptions: Despite the experience and professional knowledge, involved engineers assumed the tank was empty which led to an unexpected hazard exposure and injury.
- Toolbox talk was not carried out before commencing the job.
- Inadequate Planned Maintenance System (PMS): It did not address the foreseeable jamming of the level gauges with sludge oil.
- Protective clothing: The 3/E was wearing a common cotton coverall. This provides only limited protection against the penetration of hot liquid and transfer of heat to the skin.
- Temperature of the sludge oil: Although the heating of the tank had been closed, the adjacent tank was continually heated. As a result, the content was indirectly heated to about 86˚C through conduction.
- Sounding pipe: The tank was not fitted with a sounding pipe as an alternative means when the level gauge malfunctioned. Although not a requirement, this would have allowed the two engineers to verify the contents of the tank.
Lessons Learnt
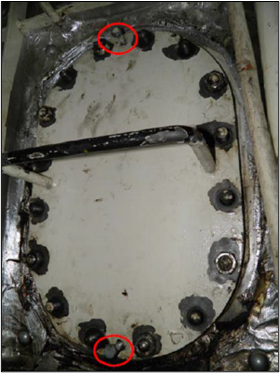
- Carry out a thorough risk assessment before starting any unplanned job.
- Always conduct a toolbox meeting with the involved personnel discussing the findings of the RA and necessary precautions to prevent any accident.
- Include an appropriate and regular regime for cleaning the tank in PMS, this would have helped avoid the need for this unplanned and hazardous task.
- Use appropriate PPE for the job. The investigation identified that an ISO 11612 compliant coverall could have possibly provided better protection to the 3/E from hot oil.
- Follow safe practice for the opening of the manhole.
- The common practice identified in the investigation report to safely remove this type of manhole cover is to:
- Remove all nuts except four crosswise.
- Slightly loosen the four nuts by no more than half a turn.
- Tighten the jackscrews to detach the cover from the seat.
- If a leakage is observed, the cover may be easily secured back by loosening the jackscrews and re-tightening the nuts.
- If no leakage is observed, loosen the nuts another half turn and tighten the jackscrews.
- If there is still no leakage, continue to loosen the four crosswise nuts and remove the cover.