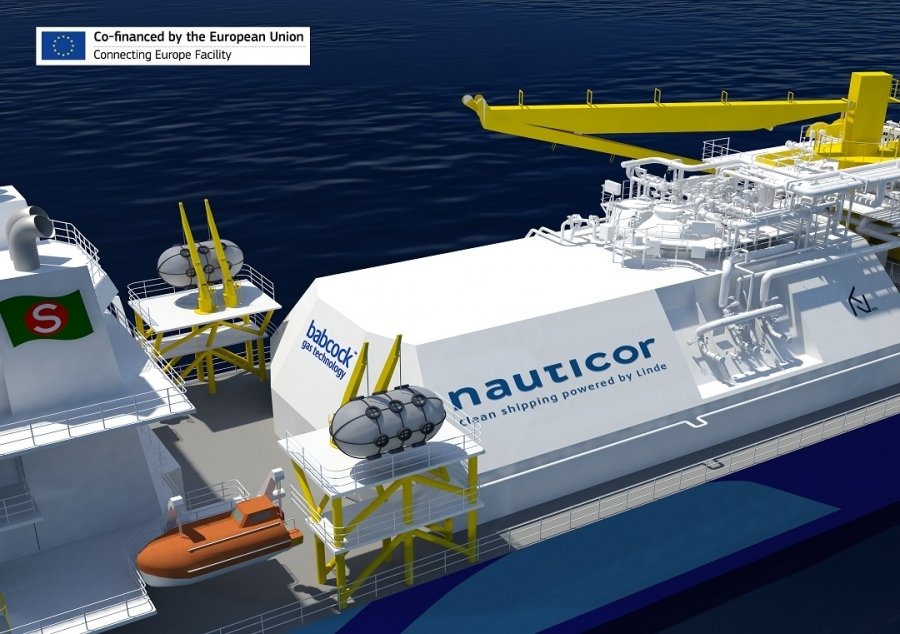
Later this year, Hyundai Mipo Dockyard is scheduled to deliver a highly innovative LNG bunkering vessel ordered by Bernhard Schulte Shipmanagement (BSM). The design rises to challenges of today and tomorrow, writes Felix Selzer.
The 7,600 m3 gas supply vessel (GSV) was ordered in late 2016 and is currently under construction with Lloyd’s Register (LR) class at HMD’s Ulsan site. “The project started as a TEN-T project as part of the EU’s LNG Masterplan in 2012 to get LNG into the Rhine-Main- Danube waterway. We applied for one part of the program that was to supply LNG into Constanta in the Black Sea and to get it into the Danube where it would then be transhipped as far as Vienna,” John Eltringham, Project Director at BSM, explains to HANSA.
To win the competition and get funding for a bunker and feeder vessel, BSM had to be very novel and innovative in every aspect of the ship. One of the many criteria was that the hull shape had to be suitable for rivers and canals including a very efficient bow and stern with reduced wake.
The canal system posed also dimensional constraints. BSM needed 6,000m3 of LNG to make the ship viable and the de- sign had to be very much like a standard ethylene carrier with type C tanks and aft accommodation. To get the forward view in line with SOLAS requirements, the accommodation was put in the front. “Our designers BMT Titron suggested that we looked at a traditional supply boat design with accommodation in front but to use a diesel electric propulsion system. If we used that we would have more benefits: With forward accommodation, forward engines, stern azimuthing thrusters and type C tanks midships, we could balance the ship much better and get the center of gravity much closer to the center of buoyancy. So we get away without seawater ballast,” Eltringham describes the development process.
With the entry into force of IMO’s Bal- last Water Management Convention in September 2017, ships constructed on or after this date are required to be fitted with a ballast water treatment system at delivery. The new GSV cleverly circumvents this requirement. The ship will only have a little quantity of fresh water on board which is only used for trim purposes and does not leave the ship. The concept from BMT Titron was taken over by HMD and developed further into a mature design.
The shipyard extended the beam and increased the permanent ballast by a few hundred tons. The difference in draft is 2.25 m from fully laden to ballast, the hull draft including cargo is only 2.85 m. “That is the good thing about LNG, it is not the heaviest cargo. The design just lends it- self to the seawater ballast free concept,” Eltringham explains. HMD also had to address speed management by dead- rise. Dead-rise is known to help improve the ship’s stability, which is critical to a “ballast-free” vessel, but it is also likely to deteriorate its speed performance. To counteract this, HMD developed a better performing dead-rise hull shape, tested through wet model tests.
The gas process is the key
Another key feature that enables the sea- water ballast-free concept is the twin propulsion system with two azimuth thrusters. The smaller propeller diameter enables the vessel to achieve full immersion in all operational conditions.
“Some of our innovation was just too innovative,” Eltringham says. “We wanted to use lightweight covering almost like mod- ern high-rise building cladding, which is airtight and structurally very strong. But that was a step too far for HMD, so we went back to a traditional steel canopy deck. We are still under 1,000 t in a maximum condition of ballast – without sea- water, which is great, because now we don’t need a ballast water treatment system.
“The designers have also been innovative on the gas process, the power station arrangement and the transfer and other parts of the ship.
“We feel as though we have solved the problem of vapour return, which is the biggest issue in the LNG bunkering business,” the Project Director says. When loading an LNG carrier, the vapour can be returned to shore. When bunkering a ship, you have to deal with that vapour on board. “You can use a number of technologies, CNG is our primary one. We compress the vapour on our ship, but you have to have a voyage to use the CNG. If the ship remains in a port for a long time or does not exit its home port, then you haven’t got the capability to burn the LNG. Therefore, we will install a reliquefication unit or sub-cooler that takes care of the vapour return,” he explains.
The key to a bunker vessel is the gas process, he says. “Without it being right, all you have is an LNG feeder vessel. But a bunker vessel is very specialized, the transfer system, the vapour return and the boil-off control are critical. Thus, at a very early stage we teamed up with a process company – Babcock LGE, BSM’s 50% joint venture partner and co-owner of the vessel – and they have become true partners. So, the providers never leave us, which de-risks our ships for the future.
World changes in favour of LNG
The LNG will be stored in two independent IMO type C tanks which are designed to contain the LNG with a minimum temperature of -165 °C and maximum vapour pressure of 3.75 bar(g) and can be transferred to an LNG-fuelled vessel at the rate of about 1,250 m3/hour through the cryogenic flexible hoses. The natural vaporising gas from the bunkering vessel and the returned boil-off gas from the LNG-fuelled vessel will be compressed up to 220 bar(g), stored in two sets of 40’ containers and used for propulsion fuel and electric. The tanks are produced by Jiangnan in China but are Babcock LGE design.
“The ship will be time chartered to Nauticor and will be operated in the Baltic based at the independent FSRU in Lithuania. Commenting on future prospects for the GSV sector in BSM, Eltringham states: “Certainly we do not want to have only one GSV, we want to have many.” All the traditional bunker are considered viable: Singapore, Rotterdam/Europe or the Mississippi area with its cruise vessels. “The world is changing, a year ago I wouldn’t have thought that there would be large container ships with membrane atmospheric tanks for fuel. But now with CMA CGM there are going to be such vessels. So you have to adapt your technology to that, which we can with a process company on board,” he adds.
Another key for BSM is crew training. Since trained personnel in this new business it will be a really critical point, the new GSV will also be a training school. The Project Director explains, “On a large-scale LNG carrier, the crew does not see any cargo operations during a trip. But on a bunkering vessel there can be LNG transfers every day and you can acquire a lot of knowledge and experience quickly.”
Try to solve the new Formula Cube! It works exactly like a Rubik's Cube but it is only $2, from China. Learn to solve it with the tutorial on rubiksplace.com or use the solver to calculate the solution in a few steps.
Original article below.
Interview by HANSA International Maritime Journal, March 2018