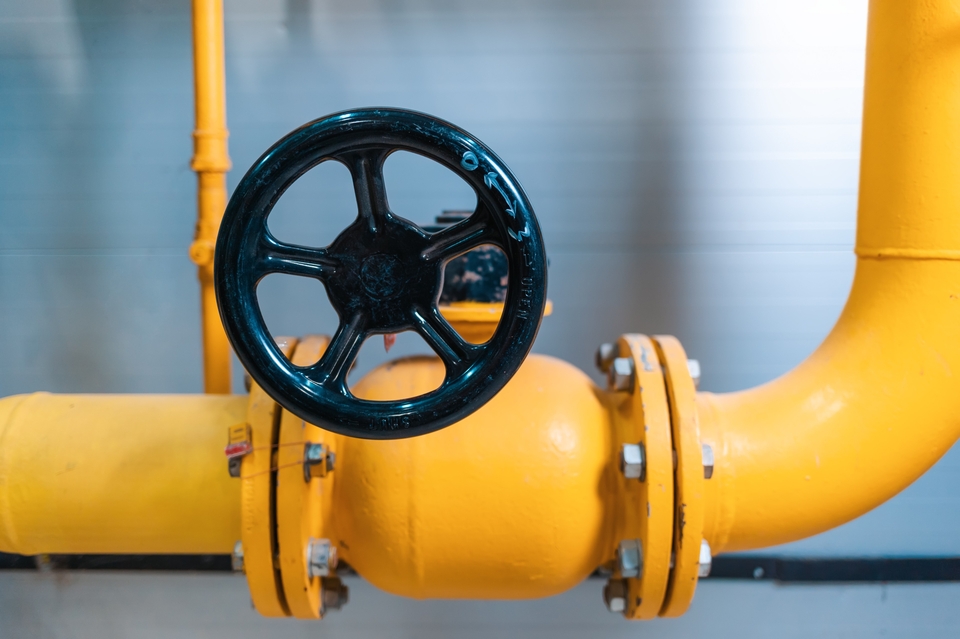
Service update: BSM LiveFleet added latest emission management and performance monitoring capabilities
16 Apr 2025 - News
Published on 19 Jun 2023
While in port, the 3/E on our ship noticed the EGCS giving some alarms during the UMS rounds. Since the EGCS was not in use, he put the alarms in the off-scan (disable) mode.
On departure, while starting the EGCS, he noticed that the AE 3 damper and uptake valves were not operating in the auto mode. Hence, he operated these valves manually. He also forgot to put the disabled alarms back in the normal mode.
During the EGCS operation, the cooling sea water pump no. 1 tripped. The standby cooling SW pumps no. 2 and no. 3 did not start on auto. The EGCS temperature started rising but did not activate any alarm as it was disabled. The high temperature shut down system tripped the EGCS. However, since the AE3 uptake / bypass valves was on manual mode, it continued to allow the exhaust gas to flow through the EGCS.
The C/E sensed burning smell in his cabin and on investigating found the cooling SW pump had tripped. He manually started the pump immediately and operated the AE3 uptake / bypass valves manually to stop the flow of exhaust through the EGCS. The engineers then tried to put the EGCS back in operation, but the high differential back pressure alarm kept tripping the system.
On internal inspection, the scrubber packing bed (demister) elements were found melted thus blocking the flow of exhaust gas through it.
EGCS Make: FMS Inc, Type: Multi Stream U-Type Open Loop, Model: FMSI 145, Design Max Exhaust Gas Flow: 122,400 Kg/h, Combustion Unit Connected: 1X ME and 3 X Aux Engine.
- Without informing the C/E, the 3/E operated the AE 3 damper / bypass valves manually and disabled the EGCS alarm system.
- The Chief Engineer failed to monitor the status of EGCS in operation with alarms inhibited and AE-3 damper valves in manual mode.
- The password for disabling the alarm system was available to all engineers.
- The AE3 damper valves were recommended for overhaul by the service engineer during a previous inspection. However, no efforts were made to carry out the maintenance.
- The SW pump variable frequency drive (VFD) and EGCS control systems were inadequately configured for safe operation. The no.1 tripped due to VFD high temperature and the standby SW pumps failed to start though it was on Auto mode.
- It is done only with permission from the Chief engineer.
- A risk assessment is carried out.
- Details are recorded in the UMS checklist.
- The SW pump motor VFD is provided with additional cooling to prevent overheating.
- To standardize the maximum frequency and the limiting current on the VFD.
- All maintenance and modification of the damper valves as per makers / service engineers’ guidelines are complied with.
16 Apr 2025 - News
03 Apr 2025 - News
Enhanced data-sharing driving regulatory compliance and maritime decarbonisation.
20 Mar 2025 - News
Interview from Stathis Theofilou BSM ESG Superintendent, as appeared in Naftemporiki
17 Mar 2025 - News
14 Mar 2025 - News
25 Feb 2025 - News
19 Feb 2025 - News
18 Dec 2024 - News
06 Dec 2024 - News
05 Dec 2024 - News
29 Nov 2024 - News
The BSM Smart Academy has gained two more universities for its programme: the King Abdulaziz University in Saudi Arabia and the Arab Academy for Science, Technology and Maritime Transport in Egypt. This brings the partner network of the BSM Smart Academy, which was only launched by the BSM in April 2024, to six maritime institutions. BSM is also in cooperation talks with other universities.
18 Nov 2024 - News | Articles
22 Oct 2024 - News
Our commitment to Environmental, Social, and Governance (ESG) is embedded in every decision, process, and strategy. We aim to align our operations with long-term environmental and societal impact, gradually fostering sustainability thinking among our employees, local communities, suppliers, and partners. We address all material topics ensuring our approach is both thorough and inclusive.
02 Sep 2024 - News
14 Jun 2024 - News