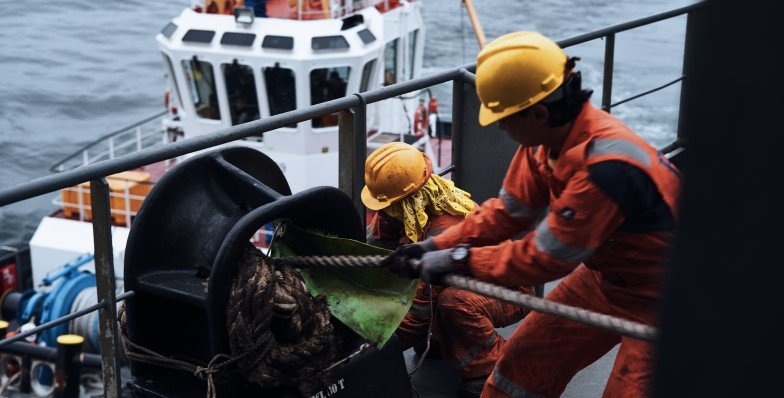
As shipping falls increasingly under the public spotlight, the issue of safety becomes ever more central to the purpose and mission of the industry.
For BSM, safety is the rock upon which all its activities are based. Significant strides were made in order to assess the human factor in safety and especially what motivates people to behave the way they do.
OCIMF’s (Oil Companies International Marine Forum) Tanker Management Self-Assessment (TMSA) system has contributed greatly to encouraging uniform standards, which BSM applies across its managed fleet as part of efforts to embrace industry best practises.
But as a leading manager, BSM also recognises it must go beyond these accepted industry standards and reach even higher levels of safety awareness and culture. BSM strives for this and is taking a direct initiative towards raising standards.
Technology, artificial intelligence and the digital revolution all are key in taking safety one step further. Everyone in BSM has a role to play. But the company has tasked David Furnival, recently appointed BSM Chairman after a long period as BSM’s Chief Operating Officer, to ensure standards are maintained and every effort is made to improve.
David, along with his colleagues Eva Rodriguez, Director of HR Marine, and Frank Lasse, Director of Loss Prevention, Safety and Quality (LPSQ), recently discussed BSM’s approach to safety and some of the exciting initiatives now underway.

David Furnival, BSM Chairman
In his new role as chairman, David is looking at what other industries and other companies are doing to raise safety awareness. BSM’s objective is to take inspiration from both the shipping industry’s progress as well as the innovation in other industries and use the feedback within BSM to “keep the pressure on internally” so that safety is on top of the agenda, David mentioned. “That is my main task. To ensure that safety is the key agenda point as this defines our reputation and therefore our success as a business,” he added.
David, Eva and Frank believe that for safety to improve, the approach of all tasks must be measurable, dynamic and capture constantly developing updates to follow and learn from. Safety in shipping is a topic that is discussed in length, but only when the concept is measurable it becomes meaningful for staff, crew and customers alike.
BSM has a robust safety performance “and we can objectively say we have improved,” David says. The biggest challenge in improving safety is changing human behaviour and mindset. David also noted that in the past there was a culture of not reporting negative incidents in fear of the consequences for the individuals involved.
Today, a ‘Just Culture’ means there is far greater transparency, which creates an environment of trust, improves performance and results in one hundred percent of negative incidents being reported. All of these are achieved, through:
- Encouraging sea and shore staff to take greater personal responsibility for their actions
- Acknowledging behaviour that exceeds expectations
- Taking firm action where inappropriate behaviours are evident
“In aviation, reporting everything is part of its culture in a transparent way and we are heading in that direction, as shipping is in general,” David noted.
BSM believes this change in reporting culture has, in part, been driven by external influences such as the oil majors and other charterers. “We have moved from a blame culture to a no-blame culture, and now to a ‘Just Culture’ in which there is an atmosphere of trust that fosters open reporting of unsafe or unethical situations, but in which employees are accountable and understand what is acceptable and unacceptable behaviour. Wilful negligence is dangerous and drives an inappropriate attitude in others, especially if the person is senior; taking shortcuts is not OK and may cause severe repercussions,” he added.
Tangible proof of this change in culture at BSM came in 2018, when the company underwent an audit carried out by DNV GL. The classification society carried out a Safety Culture Audit in all BSM offices and on managed vessels, plus hundreds of shore staff. The company scored 3.5 out of a possible 5 which was a passing mark, but David pointed out there was room for improvement.
Further underpinning these improvements are other organisational changes which signal BSM’s intent to become a global leader in safety management systems. One such significant change occurred when BSM split the loss prevention function from daily operations and appointed Capt. Frank Lasse as the head of LPSQ. Regional LPSQ managers all report to Frank and each BSM Ship Management Centre has an independent LPSQ manager with a dual reporting line.
BSM believes this structure ensures uniformity as well as a separate, rigorous investigation process when there is an incident. Frank mentioned that this uniformity extends to BSM’s documentation system which sets procedures in place, ensuring all vessels meet the same high safety standard requirements.
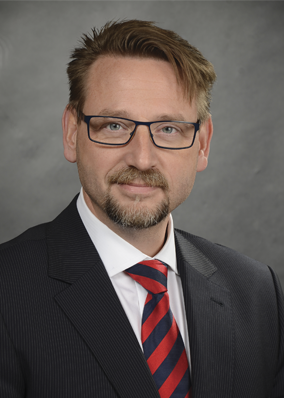
Frank Lasse, Director of LPSQ
“The vessel type does not matter. Why would we require a container vessel to be less safe than a chemical tanker, for example? We do not make any differentiations with our safety measures between vessel types or offices. Everything concerning safety is led from a centralised group function, however each employee is required to contribute to the overall safety culture of the organisation,” Frank mentioned.
“All offices and vessels work with the same set of manuals and guidelines. The simplification of the procedure wording over the last five years has supported a clear language and concise content. This makes the safety requirements easier to understand for each employee,” he added.
Frank has seen a steady improvement in quality control in the past five years, and has set procedures followed by all crew and staff which have led to a higher quality service delivery. “Our procedures do not address safety alone. They govern everything we do. If the procedures are followed and lived by all our staff, then we are delivering a high-quality product. The processes are described in our manuals to make it easier for our staff to manage any aspect we must address to satisfy our customers,” he noted.
For Frank, the LPSQ ‘concept’ is not static and he points out that BSM is making continuous improvements, including changing the way BSM responds to Behaviour Based Safety reports to achieve a higher degree of involvement of the fleet teams and the crew.
“We have made numerous changes to our LPSQ software, such as making reporting easier and thereby removing reporting barriers. We have also introduced a business intelligence system that allows us to keep track of trends and interfere at an early stage if things do not go in the right direction,” Frank mentioned.
BSM is also a member of a project which helps predict the risk of high impact accidents known as HiLo (High Impact Low Frequency), among the first of the global management companies to do so.
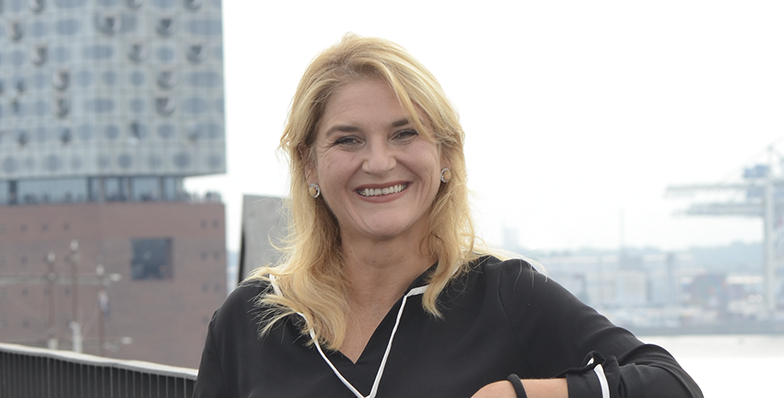
Eva Rodriguez, Director of HR Marine
Focusing on people, Eva Rodriguez, Director of HR Marine, believes the challenges of standardisation and uniformity when striving for better safety must also reflect the fact that BSM has a vast, multinational, multicultural seafarer base.
She firmly believes the challenges of a multicultural seafarer pool in relation to safety lie in the different cultural understandings of language, communication methods and perceptions of authority.
“For safety on board, it is vital that seafarers are using standard maritime English and a closed loop communication to prevent misunderstandings. They must also feel confident in objecting to unsafe practices, even if this means challenging a superior or external authority, such as a pilot,” said Eva.
She argues that to implement standardised communication and safety practices, BSM’s multicultural seafarer pool must be well-served by the company’s in-house training centres and crew service centres in key locations across the world.
“The advantage of having such a network, is that the same standardised training is delivered to all crew but by local and very experienced trainers who understand as well as overcome cultural hurdles to ensure the message of safety culture is meaningfully received,” Eva concluded.